Additive Manufacturing-Digital Systems
- Sebastian Bluemer
- Oct 25, 2022
- 2 min read
Updated: Feb 5, 2023
Good morning AM fellows,
as announced last week, today's topic is about digital systems for establishing a mass production of AM components. It is important to clarify the principle of digital manufacturing and to show the advantages of a system-based mass production. (might be possible that I missed some arrows in the sketch 😉)
Focus of the sketch below is on printing components. At first a new customer order reaches the operations department which is processed and planned using a MES. Subsequently, a required workflow is defined in order to successfully manufacture the AM component - Print - HT (heat treatment) - PP (post processing) - possible to use a ERP system over here. The job data is created and then transferred to the machine software of the L-PBF printer. During printing, machine status and sensor data can be transferred to ensure consistent monitoring of manufacturing your AM products.
After printing, the build plate will be removed and screened for completeness. Subsequently, the components are individually analyzed on the build plate using quality assurance methods and their status is transferred to a Quality system (QS). The MES can now be used to decide directly whether or not it is necessary to reprint individual components.
The system landscape (map below) is essential for processing serial jobs, as otherwise documentation of the component status cannot be guaranteed. In our conventional sinter business, I quickly learned that without systems, you can easily lose track of the status focusing on individual components and by approaching mass production you are not able to follow components anymore.
What is your experience with a digital system landscape for additive manufacturing? Do you use monitoring systems in your everyday work and do you consistently document the status of components?
I am curious about your experience!

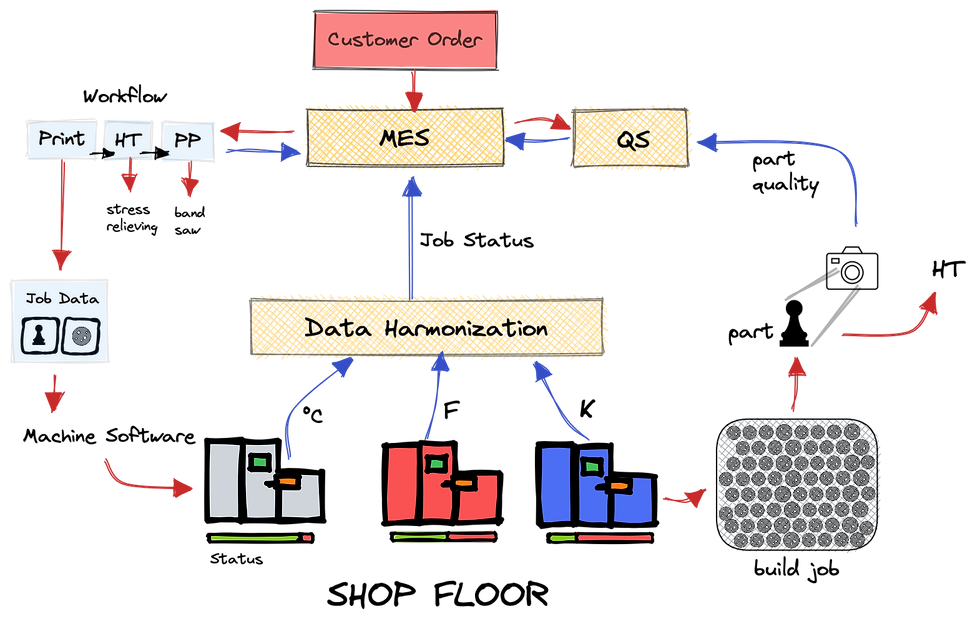
Comments