Check the "AM-Playbook" for Artificial Intelligence
- Sebastian Bluemer
- May 5, 2023
- 4 min read
Updated: Jun 9, 2023
Artificial Intelligence (AI) is playing an increasingly important role in the field of engineering. As engineers, we are slowly accepting the fact that we have an additional tool in our digital toolbox, which we will use more frequently in our daily routine. AI already has a significant impact as a daily co-pilot during our work in research, daily communication and as a second brain (kind of idea collector).
So, how can AI be used in the field of Additive Manufacturing (AM)? I would like to answer this question in the next blog posts and give you some examples from a design, process preparation, laser parameter and monitoring system perspective with a strong focus on the manufacturing strategy - Laser Powder Bed Fusion.

Design
Additive Manufacturing is very well suited for new design approaches due to the near net shape manufacturing strategy and the need to achieve a functional advantage due to higher production costs compared to conventional manufacturing strategies. Simply adapting a conventional design for AM does not make sense at all, and I think most of us already know that.
How far away is AI from becoming our daily Co-Pilot in Additive Manufacturing?
We must think outside the box to benefit from Additive Manufacturing. AI can be an opportunity to develop a new approach for design modification. So let us understand how we can use AI for specific designs supported by computational algorithms.
Overview
First, technical requirements must be defined and translated into a digital question. Issues such as flow optimization, mechanical strength, design structural properties of parts are just a few examples that can be considered for AM applications. Since we are using a near-net-shape manufacturing process, we can benefit from an increased design flexibility.
Let's focus on optimizing the flow conditions within an L-PBF manufactured manifold and define this as a target scenario to further understand the potential and capabilities of AI in a second step.
Define Boundary Conditions
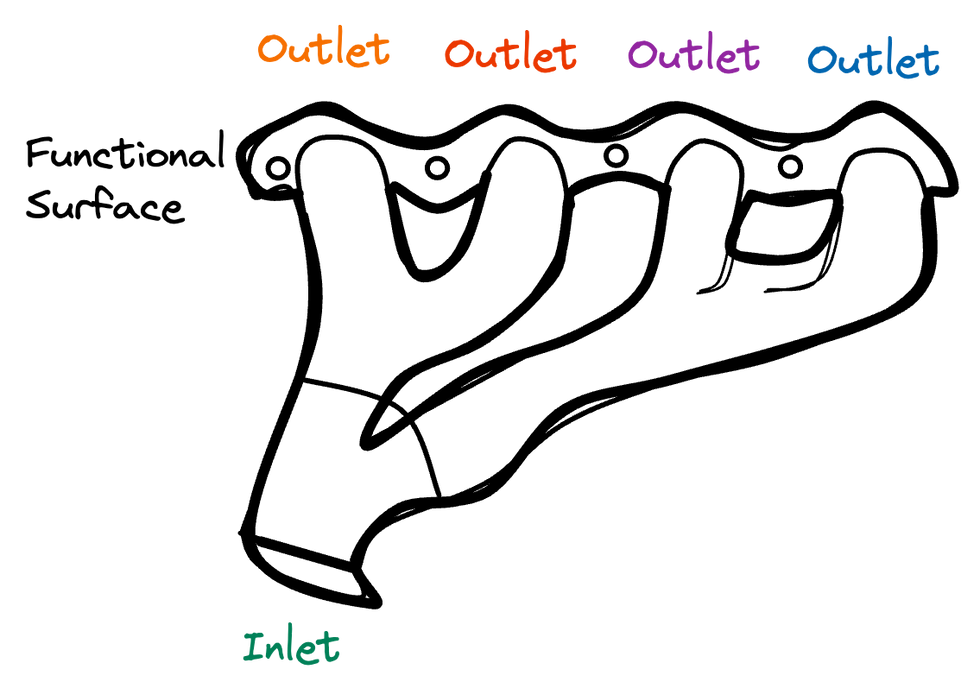
Inlets and Outlets are defined based on requirements, focusing on the later application. Since we need them for post-processing, functional surfaces are also predefined. These predefinitions of functional require- ments are made by engineers and a basis for AI algorithms in a second step.
Once the boundary conditions are in place, the next step is to understand which kind of tools would be able to optimize the flow within a manifold. Since we do not have a printed prototype with a customized digital interface to track flow conditions yet, we need a software capable for flow simulation (e.g. Computational Fluid Simulation - CFD).
Simulation and Predictive Flow Analysis

Sure, a simulation software tool is suitable for solving problems through computational calculations and it is nothing special as we as engineers have been preparing such an environment for years. Building an AI-ready environment for simulation with a detailed predictive flow assumption will be a new challenge, and that is what we as engineers are looking for.
After a successful simulation of our part, we get a first tendency of possible turbulence within our manifold (red). This procedure covers one of our first options to solve the flow optimization problem, but it is not yet what we are looking for, as we want a detailed predictive flow analysis that covers the actual flow situation as closely as possible.
Printing a prototype for testing and sensor measurements would be a chance to monitor the flow inside the manifold in a second step. At this stage, L-PBF can be used to print these parts as it offers short lead times and the ability to produce parts with high design flexibility in an early testing stage. The printed parts can then be used for subsequent testing, such as additional flow measurements.
Sensor values from the prototype and the simulation provide us with a huge amount of data that needs to be handled carefully. AI can help us align both types of data with a focus on our initial flow optimization problem.
The simulation software company Hexagon is already able to combine both simulation and actual sensor data and generate a predictive model using AI algorithms. (1) "Odyssee as a software platform applies both AI and ML to real-world sensor data and physics-based simulation data to generate accurate, predictive models of a product," Hexagon says on its website.

Design Modification

Flow optimization studies give us the opportunity to think about part design, as this can be one of the key factors. Since we have our prototype test setup and simulation model, we can predict a more detailed flow for our later application, and even better, we can use the developed test setup for design modifications as well.
Laser Powder Bed Fusion is a near net shape manufacturing strategy that can be used in an environment where quick design changes have to be made. Since we have a part equipped with sensors and a simulation model, we can use both to modify the design of our initial manifold. The boundary conditions (inlets and outlets, functional surfaces) were predefined at the beginning, so let's start using AI and see what kind of design changes can help optimize the flow even further.

Summary
"How far away is AI to becoming our daily Co-pilot in Additive Manufacturing?" In today's blog post, I wanted to teaser an opportunity to use AI based on a design modification challenge. AI can support to achieve a more detailed analysis and handling of different data from various instances, opening up a new way of design modification. It helps us to think outside the box faster and identify new opportunities as a kind of "co-pilot" in the design department. However, AI is still a new feature in the Additive Manufacturing industry, and gatekeepers such as standards also need to be adapted to this tool before we can use it for critical applications.
What do you think about AI as a tool to generate designs for Laser Powder Bed Fusion processes?

Comments